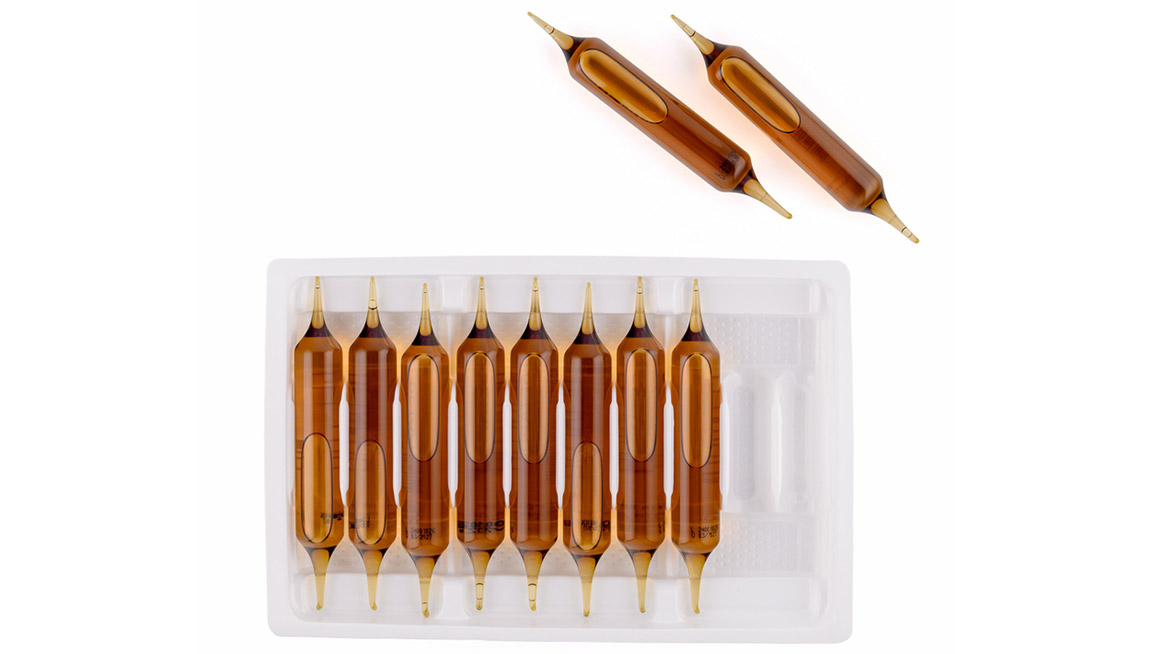
Headquarters and industrial site
Route de Bordeaux
47700 Casteljaloux
France
Commercial office
18-22 rue Marius Aufan
92300 Levallois-Perret
France
The primary function of medical packaging is to protect the pharmaceutical products and to ensure that is stored correctly. It also plays an essential role as an information medium (labelling, leaflet) to promote patient compliance and help fighting against medication errors. The choice of primary and secondary packaging is therefore a real strategic driver for pharmaceutical companies.
The primary function of medical packaging is to protect the pharmaceutical products and to ensure that is stored correctly. It also plays an essential role as an information medium (labelling, leaflet) to promote patient compliance and help fighting against medication errors. The choice of primary and secondary packaging is therefore a real strategic driver for pharmaceutical companies.
There is a lot of packaging solutions for medical products:
The most common packaging materials are glass, plastics (flexible or rigid plastic), paperboard and metal (aluminium). Selecting the right packaging solution and material depends on different factors such as:
The ampoule is a perfectly sealed packaging which offers many advantages for drugs manufacturers.
The double-tip ampoule is perfectly hermetic and ensures the product’s stability and safety. Made of pharmaceutical glass, this protective packaging is highly resistant to high temperatures and to most chemicals. As an inert and non-polluting component, glass prevents the transfer of particles between the container and its content. It is also infinitely recyclable. Thus, glass packaging is considered less toxic than metal or plastic packaging.
Double-tip ampoules are an economical solution with a very competitive filling cost thanks to a vacuum suction process invented by SFAM. They are autoclavable which allows sterilization after filling and sealing.
As a unit-dose packaging, drinkable ampoule facilitates compliance with treatment by ensuring that the correct doses are taken and guarantees use without risk of contamination.
Initially intended for drinkable healthcare products, double-tip ampoules are now available in various sectors of activity such as food supplements, nutri-cosmetics, veterinary products and other industries.
Packaging production can include different processes from extrusion to injection molding, blow molding or glass molding.
For more than 70 years, we have specialized in the manufacture of double-tip ampoules. The filling and heat-sealing processes are conducted by our customers.
Our ampoules are created from ILLAX® (Type III) or FIOLAX® (Type I) glass tubing. Those tubes are molded into double-tip ampoules on our automated production lines.
First, the carousels are filled with glass tubes. The burners shape the ampoule from tip to tip and heat-seal one side. The ampoules can then be printed according to customers’ request. Our silk-screening process only uses colours without heavy metals that are resistant to chemicals and solutions. The next step of the process is the vitrification.
Finally, the Double Ring Break is applied. DRB process was invented and patented by SFAM. It pre-determines the breaking point which considerably reduces the risk of glass particles being released on opening the ampoule.
The ampoules are packed on plastic boxes, stacked on pallets and delivered to customers in the pharmaceutical industry filling and heat-sealing.
To reduce our environmental-impact, and our customers’, the plastics trays are reusable: they can be collected and recycled.
We meet all the pharmaceutical packaging manufacturing requirements. Every single ampoule we manufacture is subject to quality-control and is automatically and visually checked. In addition to this, the typical statistical checks are carried out to ensure the highest level of quality. We are also certified ISO 15378 and ISO 9001.
To meet the specific demands of our customers, we carry out feasibility studies.