- Accueil
- Nos actualités
- La fabrication des ampoules double pointe en verre à usage pharmaceutique / nutraceutique
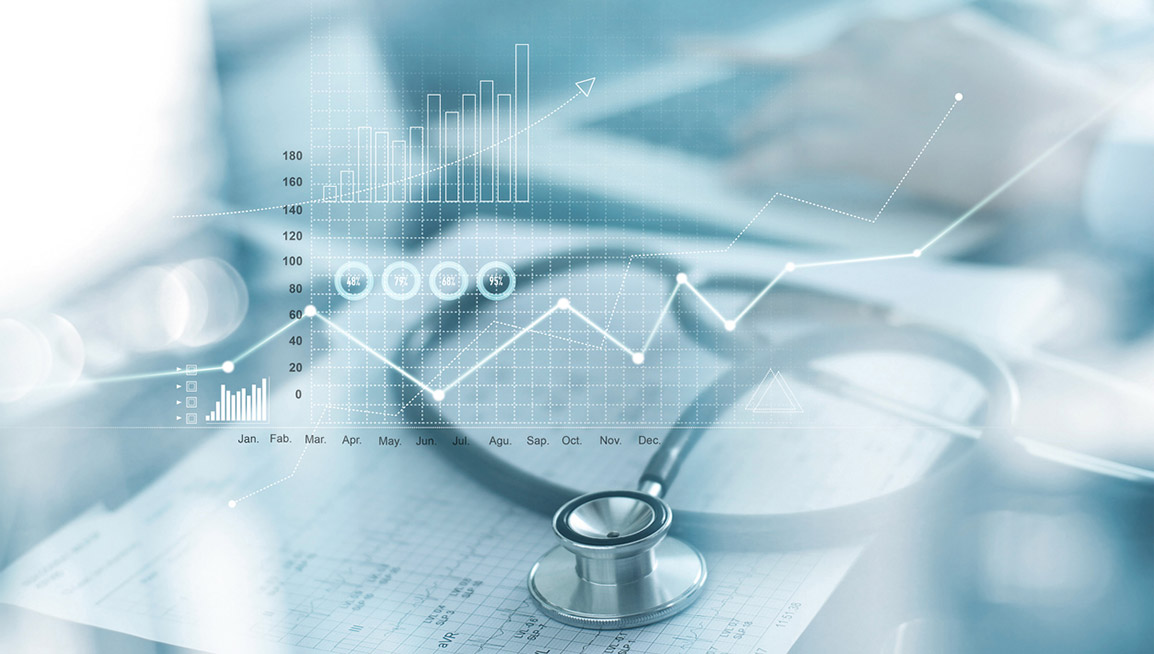
Les ampoules deux pointe en verre, d’une capacité comprise entre 1 ml et 20 ml, sont fabriquées dans une verrerie telle que la SFAM, et livrées vides au laboratoire client qui les remplit et les scelle. L’ampoule deux pointes en verre est un emballage primaire, c’est-à-dire un emballage qui est directement en contact avec le principe actif du médicament ou du complément alimentaire.
Les ampoules deux pointe en verre, d’une capacité comprise entre 1 ml et 20 ml, sont fabriquées dans une verrerie telle que la SFAM, et livrées vides au laboratoire client qui les remplit et les scelle.
La fabrication d’une ampoule double pointe en verre consiste à :
L’ampoule deux pointes en verre est un emballage primaire, c’est-à-dire un emballage qui est directement en contact avec le principe actif du médicament ou du complément alimentaire. De ce fait, la composition du verre dont sont constituées les ampoules est réglementée par la pharmacopée.
La Pharmacopée européenne prévoit, pour les récipients, les types de verres suivants :
Un verre est dit neutre lorsque, dans le temps, il libère très peu d’ions sodium (notamment) dans le liquide qui est à l’intérieur du récipient. Le verre ordinaire, sodo-calcique, n’est pas neutre au sens de la pharmacopée. Le verre type I est un verre borosilicaté, qui dégage environ dix fois moins d’ions sodium que le verre sodique.
Pour les ampoules en verre pharmaceutiques, on parle aussi de verre jaune 2e classe, à ne pas confondre avec le verre de type II. Il s’agit d’un verre « semi neutre », dont le dégagement est nettement inférieur à celui du verre ordinaire, qui est généralement réservé aux ampoules buvables.
En effet, le traitement de surface ne s’applique pas aux ampoules en verre, mais uniquement aux flacons (à quelques rares exceptions près).
La matière première utilisée pour fabriquer les ampoule deux pointes en verre est un produit semi-fini : la canne de verre. Cette canne de verre, réalisée par étirage-soufflage en sortie de four de fusion, est livrée à la verrerie de transformation, telle que la SFAM, sous forme de tronçons d’environ 1,5 m de long, qui sont déjà au diamètre et à l’épaisseur de l’ampoule à réaliser. La verrerie de transformation produit les ampoules en verre par étirage de ces cannes, afin de former les deux pointes.
Deux types de verre sont principalement utilisés pour les ampoules en verre :
L’ampoule double pointe en verre est fabriquée sur des machines verticales. Elle est livrée au laboratoire client avec une pointe fermée (la pointe perlée) et une pointe ouverte (la pointe coupée), qui sera ensuite scellé par le laboratoire après remplissage.
La vidéo sur le site de la SFAM permet de comprendre le processus de fabrication décrit succinctement ci-après.
La machine verticale est un carrousel sur lequel on dispose de 24 à 36 cannes de verre, grâce à un robot « chargeur automatique » qui permet de positionner les cannes de verres verticalement sur le carrousel qui est en rotation permanente. Une série de chalumeau permet ensuite d’étirer les cannes pour permettre la formation des deux pointes au fur et à mesure que les cannes tournent autour du carrousel et descendent par gravité. Un couteau permet de rompre l’étirement de la canne pour former les pointes, et un dernier chalumeau permet de fermer (perler) une des deux pointes en la réchauffant légèrement.
On fabrique dans le même cycle la pointe coupée d’une ampoule en verre (dont la pointe perlée a été réalisée au cours du tour précédent) et la pointe perlée de l’ampoule suivante. De ce fait, on a une chute de début de canne qui comporte uniquement une pointe coupée, puis une chute de fin de canne qui n’a qu’une pointe perlée.
Enfin, les ampoules en verre terminées sont récupérées sur un tapis convoyeur pour les opérations de finitions.
Le savoir-faire du régleur verrier consiste à doser la chauffe de chaque chalumeau, à contrôler les courses et vitesses de descente, ainsi que les vitesses de rotation de la machine et des cannes, afin d’assurer la conformité dimensionnelle de l’ampoule en verre et en particulier :
Les différentes opérations de finition sont les suivantes :
Outre la capacité, deux côtes dimensionnelles sont essentielles sur une ampoule en verre :
Ces deux paramètres sont vérifiés automatiquement en début de ligne de finition, par un système de contrôle par « dispositif de vision ». Une caméra numérique transmet une image de chaque ampoule en verre défilant sur la ligne à un micro-ordinateur. Un logiciel spécialisé analyse cette image et en déduit certaines cotes qu’il compare aux valeurs limites qui lui ont été fournies. Ce dispositif permet de contrôler, en plus, d’autres cotes que celles indiquées au paragraphe précédent.
Le système commande un éjecteur qui élimine toutes les ampoules en verres hors tolérance vers un bac à déchet unique, mais en contrepartie, l’écran indique en permanence la valeur moyenne des cotes mesurées, le nombre de rebut et la valeur mesurée sur les ampoules rebutées. C’est donc à partir des informations dont il dispose à l’écran que le régleur effectue ses corrections.
L’impression des ampoules en verres comporte notamment les inscriptions souhaitées par le laboratoire client. L’impression est réalisée par sérigraphie, en utilisant un émail vitrifiable qui devra donc être cuit.
À partir de typons (film transparent imprimés en noir), on réalise les écrans sur lesquels l’émail vitrifiable est déposé. L’ampoule en verre est levée de la chaîne par un pied de biche munis de galets. Elle vient se positionner sous l’écran qui est animé d’un mouvement de translation alternative synchronisé à la chaîne. C’est donc l’écran qui entraîne l’ampoule en rotation alors que le râcle va faire passer l’émail au travers des mailles.
On imprime une ampoule en verre dans le mouvement de l’écran de gauche à droite, et l’ampoule suivante dans le mouvement de retour. De ce fait, si la course de l’écran est mal réglée, on obtient une ampoule sur deux bien imprimée et une sur deux mal imprimée. Les contrôleurs sur ligne de finition d’ampoules et les opératrices contrôlent donc toujours deux ampoules de suite pour s’assurer de la qualité de l’impression.
L’émail des ampoules en verres imprimées nécessite une recuisson, et il en est de même pour l’émail utilisé dans le procédé d’autocassable (voir infra).
La recuisson s’effectue dans une arche qui est un four tunnel dans lequel les ampoules en verres cheminent. La température est de l’ordre de 600°C et la durée de recuisson dépend de la vitesse de défilement des ampoules et de la longueur de l’arche.
Si la recuisson est insuffisante, il pourra subsister des tensions internes, détectables au polariscope et/ou, l’impression ne tiendra pas. À l’inverse, si elle est trop forte, on risque de déformer les ampoules en verres (on dit souvent : de les mettre en banane).
À l’origine, les ampoules en verres n’étaient pas autocassables. Les ampoules pleines étaient livrées avec une lime dans chaque boîte.
Afin d’éviter l’usage de cette lime, différentes techniques d’autocassable ont été développées. Ces autocassables doivent être suffisamment fragiles pour que l’ampoule en verre puisse s’ouvrir sans difficulté, et en même temps suffisamment solides pour que l’ampoule résiste au transport, au remplissage, à la fermeture, au conditionnement (mise sur chevalet puis en boite), etc.
La maîtrise de cette force de rupture (effort nécessaire pour ouvrir l’ampoule en verre) est la principale difficulté de la réalisation d’un bon autocassable. De plus, il ne doit générer aucun risque de fuite ou d’entrée d’air dans l’ampoule remplie et fermée, et ne pas dégager de particules de verre lors de l’ouverture.
La SFAM utilise deux procédés pour assurer l’autocassable, dont un qui a été développé et breveté par elle-même :
En bout de chaine de fabrication, après le prélimage et la recuisson, les ampoules en verre sont disposées dans des cristallisoirs en polypropylène, grâce à des machines automatiques « emballeurs automatiques ». On compte de 110 à 504 ampoules en verres par cristallisoir suivant la capacité des ampoules.
Les ampoules en verre sont livrées au laboratoire client dans les cristallisoirs, pointe ouverte en haut, et ce dernier assurera le remplissage des ampoules ainsi que leur scellage.
Outre les contrôles automatiques sur ligne cités plus haut, un contrôle visuel de l’impression est effectué régulièrement, à fréquence définie, par :
Le QDP prélève, lors de son passage sur chaque ligne, quelques ampoules en verres pour contrôler l’ensemble des caractéristiques de l’ampoule dont la force de rupture des autocassables.
Tout le long du lot, on effectue des prélèvements statistiques. Le rapport de contrôle accompagnant le lot d’ampoule en verres est rédigé à partir des mesures effectuées sur ces prélèvements.
Les ampoules en verre sont livrées au laboratoire client dans les cristallisoirs, pointe ouverte en haut, et ce dernier assurera le remplissage par le vide des ampoules ainsi que leur scellage, puis leur stérilisation éventuelle.
La machine à remplir se compose d’une cuve à vide ouverte sur la partie supérieure et munie d’un couvercle pivotant. Sur ce couvercle, sont fixés des grilles destinées à maintenir les ampoules en verres lorsqu’on retournera l’ensemble (le cristallisoir et toutes les ampoules qu’il contient) dans la cuve.
On retourne l’ensemble, et on ferme le couvercle. Les pointes d’ampoule baignent dans le liquide à remplir (médicament, complément alimentaire, etc), et l’on fait le vide dans la cuve. L’air contenu dans les ampoules en verres est évacué, et par capillarité le liquide remplit l’ampoule. On ouvre le couvercle et l’on retourne de nouveau le cristallisoir qui, une fois dégagé de la grille, sera dirigé vers la ligne de lavage des pointes et de scellage.
Par ce procédé, toutes les ampoules en verres sont remplies dans le même cycle au même volume.
Le lavage des pointes est obtenu à l’aide de douches d’eau froide et d’eau chaude convenablement disposées. Le principe est de jouer sur la dilatation de l’air qui se trouve entre le produit et l’extrémité de la pointe. Les cristallisoirs d’ampoule en verres pleines circulent sur un convoyeur, sous ces douches.
Un brûleur faible, ou un réflecteur dirigeant la chaleur de la flamme de scellage qui est un peu plus loin sur la ligne, permet de sécher la pointe avant de la sceller.
Après lavage, les ampoules en verres, toujours rangées dans leurs cristallisoirs, défilent sous la rampe de scellage, qui est un brûleur air/gaz/oxygène. Cette flamme vient lécher le bout des pointes coupées qui se referme naturellement.
La stérilisation peut être effectuée par tyndallisation ou autoclavage, afin d’éliminer les formes végétatives (bactéries) et les formes de résistance (spores). Il s’agit de soumettre les ampoules en verre à des cycles de chauffage suivant le procédé choisi.
Un contrôle visuel après stérilisation permet d’éliminer les ampoules défectueuses avant de diriger les autres vers la ligne de conditionnement sur laquelle elles seront mise sur chevalet, et ces derniers seront mis sous étuis (emballage secondaire).